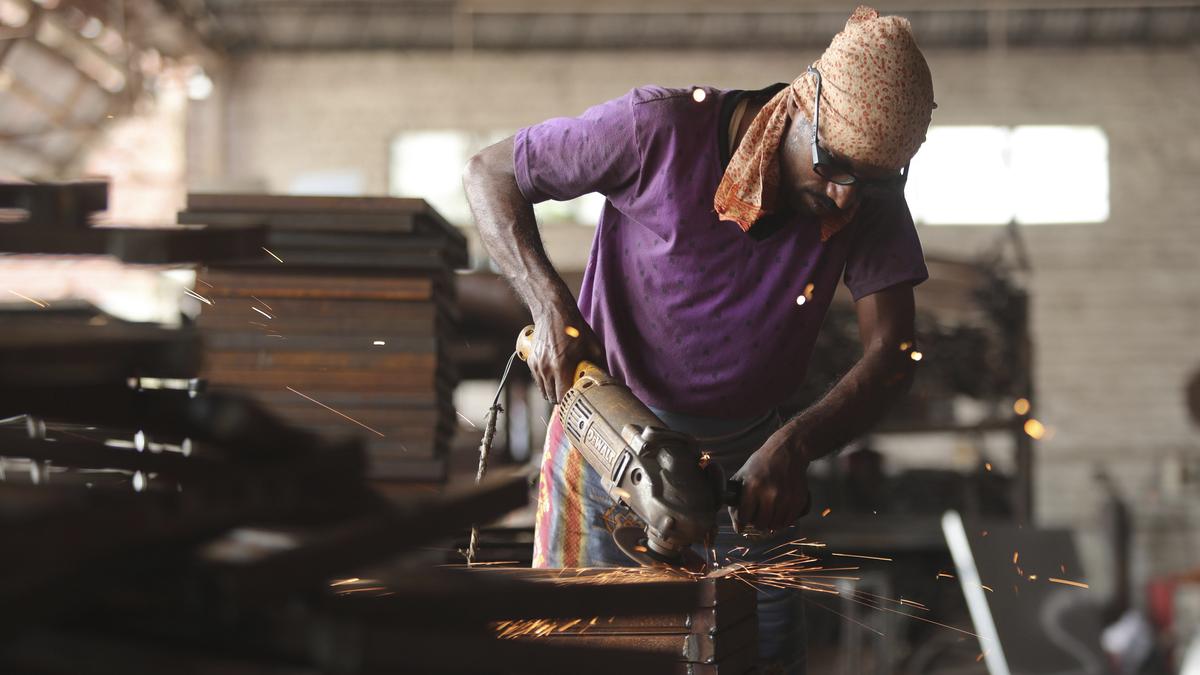
Indian industry needs innovation, not mindless toil Premium
The Hindu
India’s capitalists have deployed one strategy after another to ensure that they have at their disposal a large labour force willing to work long hours for low wages
A few months ago, this writer and his colleagues interviewed migrant industrial workers in Ludhiana, Punjab, for a research project. The respondents worked in factories (producing garments, auto components, and other products) for 11 hours to 12 hours a day. When orders were high, they worked for days on end without a break. Away from the shop floor, their waking hours were spent almost entirely on cooking and in their daily commute.
It is puzzling that some of the well-known corporate leaders in the country have been urging Indians to work longer hours. They may not be aware that most of India’s workers are informal and must work extremely long hours, sweating to earn a living (manual workers or household helpers). In 2023-24, the Periodic Labour Force Survey showed that only 21.7% of India’s workers were in regular jobs with a salary, while the rest were casual workers or self-employed. Even within the category of regular workers, approximately half of them had to face informal working conditions (they did not have a written job contract, were not eligible for paid leave, and did not receive any social security benefit).
By publicly expressing their preference for having longer working hours, industry bosses have inadvertently confirmed a well-known, yet not-much-discussed, fact. Indian industry continues to derive its competitive advantage mainly from cheap labour rather than technology and innovation. In the developed world, the mode of surplus extraction underwent a transformation long ago, from making workers labour longer hours to employing them more efficiently with superior technologies and management practices. Based on workers’ conditions during the Industrial Revolution in Britain in the 18th century, Marx wrote: “In its …werewolf hunger for surplus-labour, capital oversteps even the merely physical maximum bounds of the working day. It steals the time required for the consumption of fresh air and sunlight. It haggles over a meal-time….”
However, working conditions in Britain improved by the middle of the 19th century, following regulations brought about by labour union pressures and the sweeping economic and technological changes (although exploitative labour practices continued unabatedly in the colonies). Today, workers in rich countries put in much fewer hours but have significantly higher productivity than those in developing countries. According to data reported by the International Labour Organization (ILO) in 2024, an employee’s average weekly work hours was 38 hours in the United States and 36.6 hours in Japan as compared to 46.7 hours in India.
India’s capitalists have deployed one strategy after another to ensure that they have at their disposal a large labour force willing to work long hours for low wages. Big businesses in India have abetted a structural shift in industry from the organised sector, which is governed by regulations of wages and working conditions, to the unorganised sector, where such rules do not apply. In industrial clusters across the country, there is a predominance of small units with six or less workers. At any time in a crowded industrial area in Coimbatore or Ludhiana, one hears the sounds of several hundreds of machines (lathes, milling and rolling machines, foundries) operating in small sheds. Each shed produces a small part or a component that feeds into a production network coordinated by more prominent firms to manufacture a range of products, including pumps, automobiles, and agricultural tools. In most small firms, the owners, often former workers, work alongside the hired labourers. Over 70% of India’s manufacturing workforce (68 million in 2021-22) are in small, unregistered enterprises (each with less than 10 workers).
The relations between the small and large firms in India have not been mutually enriching (of the kind that prospered in Japan), but instead, have been enfeebling the small firms even more. In interviews this writer had with them over the years, the owners of small firms highlighted issues relating to payments for the parts or components they supply. The bigger firms typically delay these payments several months after receiving the supply, leaving the small-firm owners desperate for fresh funds to run their factories. The big firms refuse to pay more for the parts despite increases in material and other production-related costs, encouraging a race-to-the-bottom competition among the small firms. All these are at a time when small firms are weakened by inadequate state support, especially bank credit, and rising competition from cheaper imports.
India’s factories are increasingly dependent on workers who are employed through contractors rather than those they directly employ. Of all workers who joined India’s factory sector after 2011-12, 56% are contract workers. These workers, who are not protected by labour regulations, are paid much lower wages than directly employed workers. Workers who migrate from their villages to seek jobs in distant lands form the core of the labour supply for Indian industry.

The Karnataka government has drafted a comprehensive master plan for the integrated development of Kukke Subrahmanya temple, the State’s highest revenue-generating temple managed by the Hindu Religious Institutions and Charitable Endowments Department. The redevelopment initiative is estimated to cost around ₹254 crore and aims to enhance infrastructure and facilities for devotees.