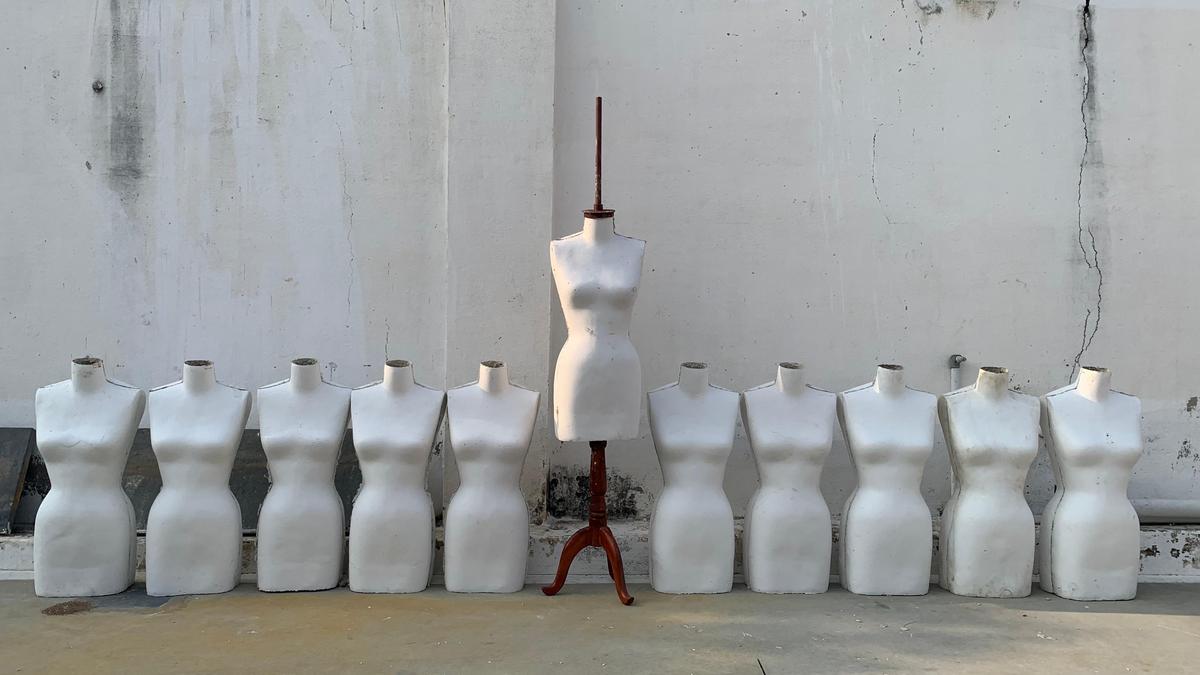
Cotton scraps turn biodegradable mannequins at Jothi Speciality Papers
The Hindu
Erode’s Jothi Speciality Papers gives cotton scraps a new lease of life by turning them into biodegradable mannequins
A few days ago, a video on Erode-based Jothi Speciality Papers — that highlighted its project crafting biodegradable mannequins — went viral on Instagram. If you have been wondering how this project came to be, here is the brand’s backstory.
Helmed by Mani P and his wife, the company has been creating recycled cotton rag paper from textile scraps since 1996. “In 1994, we visited a garment factory in Tirupur, saw a lot of waste textile fabric that ended up in landfills, and realised there were several other factories disposing of excess fabric waste. We decided to convert this waste fabric into recycled cotton paper. We also wanted to ensure the paper is used in the same textile factory for their packing, price tags, etc.,” says Mani, adding that their firm is Global Recycled Standard (GRS) certified, a tag ‘given to companies that meet stringent criteria for recycled content, social and environmental practices, and chemical restrictions in the manufacturing of their products’.
In 2010, Mani and his team were approached by jewellery brand Tanishq with a unique request. They wanted eco-friendly jewellery display busts to replace their existing plastic or fibre counterparts. “We researched for a year to create these display stands from scrap cotton fabric,” says Mani, who regularly supplies handmade paper to Bengaluru, which led to the call from the jewellery brand.
Ayil Raghavan, Senior Manager-Visual Merchandising, Jewellery Division, Titan Company, says the collaboration came about when they started sourcing handmade paper from Mani for the company’s stationery. “After visiting their set-up and studying their process, I, along with Ajay Kumar BV, deputy group manager at Titan, decided to experiment with crafting eco mannequins, and have developed them with their assistance. Today, we source 20,000 mannequins annually for Tanishq’s 500 outlets across India.”
After supplying these stands for over a decade, Mani and his team wanted to do more to address the issue of plastic waste in the industry. “In 2023, we heard that there are ‘mannequin graveyards’ where used figurines are discarded. We researched for six months and in 2024 created a mannequin made using recycled waste textile fabric,” he says.
The process to craft a mannequin begins with the brand sourcing fabric waste from garment factories in the region. “Leftover cotton fabric from the making of apparel, toy covers, mats, etc is collected by us and turned into pulp. This pulp undergoes a 30-step process including mixing the pulp with a natural and biodegradable glue, moulding, etc. to craft mannequins,” explains Mani. Each of the figurines is handcrafted by an all-women team, and it takes two people a week to make one. “They are naturally dried as using machines might damage their form, and this process takes two-three days.”
Taking us through the process, “Each mannequin can last up to five years, and two-three years if used roughly,” says Mani, adding that they are priced between ₹5,000 and ₹25,000, depending on the size. “We recycle above 100 T-shirts (25-35 kgs of textile fabric waste) to make one mannequin. They are 20% lighter in weight than plastic/fibre variants, are anti-bacterial and anti-fungal, and can be customised.” Ayil explains that they earlier used fibre mannequins. “The eco variants are light-weight, and sustainable. Although they are expensive and need to be changed every few years, their environmental benefits outweigh these concerns.”

Thomas Jefferson and Abraham Lincoln are two of the greatest presidents that the U.S. has seen. You probably know that already. But did you know that Jefferson made what is considered the first contribution to American vertebrate paleontology? Or that Lincoln is the only U.S. president to receive a patent? What’s more, both their contributions have March 10 in common… 52 years apart. A.S.Ganesh hands you the details…