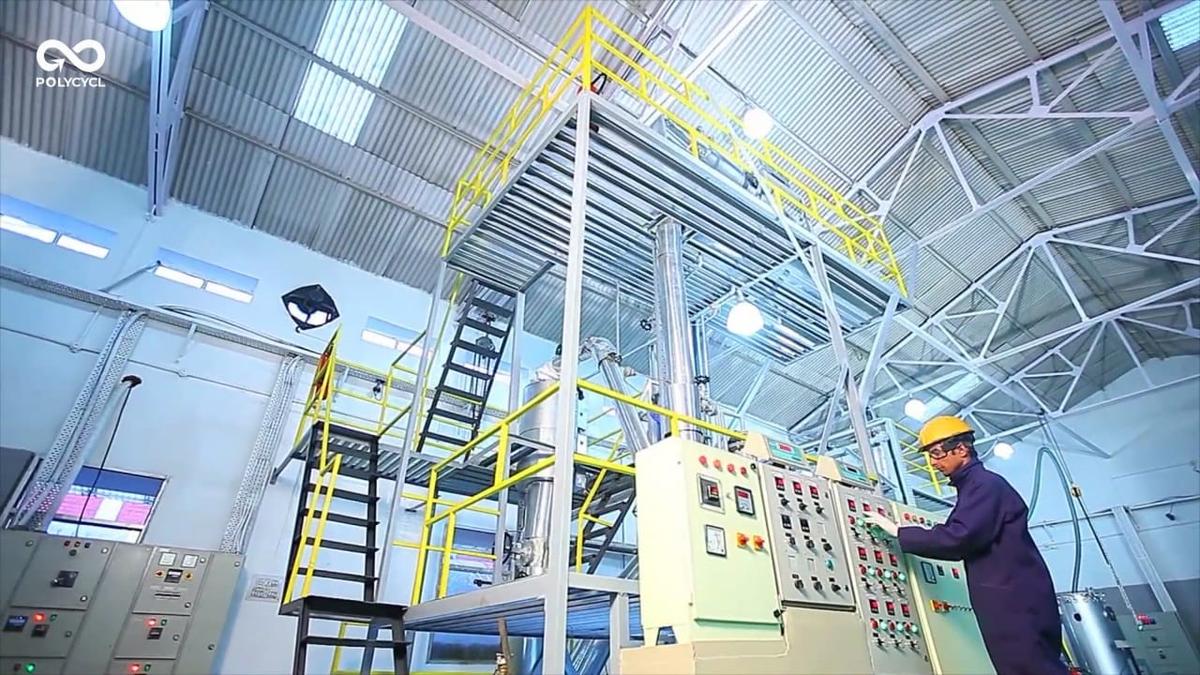
Chandigarh start-up announces launch of unique plastic recycling technology in Bengaluru
The Hindu
According to the company, the technology, protected by multiple international patents, facilitates the creation of a plastic-to-plastic circular economy, where commonly used plastics such as polyolefin packaging no longer need to be down-cycled, incinerated or landfilled at the end of their life. Instead, they can be continuously recycled in a closed-loop, without any loss of quality.
PolyCycl, a circular economy technology start-up based in Chandigarh, today announced the launch of its patented technology that enables conversion of hard-to-recycle plastics into food grade polymers, renewable chemicals and sustainable fuels.
The fully indigenous Contiflow Cracker Generation VI chemical recycling pyrolysis technology, which comes after a decade of research and development, helps to address the waste management of items such as single-use grocery bags and food-contaminated packaging.
According to the company, the technology, protected by multiple international patents, facilitates the creation of a plastic-to-plastic circular economy, where commonly used plastics such as polyolefin packaging no longer need to be down-cycled, incinerated or landfilled at the end of their life. Instead, they can be continuously recycled in a closed-loop, without any loss of quality.
This is done through a process where low-grade plastics are transformed into liquified hydrocarbon oils, which are then purified to remove contaminants like halogens and hetero-atoms. The resulting chemical feedstocks can be used by the petrochemical and hydrocarbon industries to produce a wide range of premium low-carbon materials, including circular polymers. In other words, the technology allows to turn low-grade waste plastics into a resource for manufacturing new materials.
“India generates over 10.2 million tonnes of plastic waste annually, with more than 40% of this being single-use plastics like grocery bags and flexible packaging. Traditional recycling methods struggle to handle this waste, which often ends up clogging drains, littering streets, or polluting waterways” says Amit Tandon, Founder and CEO of PolyCycl.
“PolyCycl’s technology offers a novel solution for recycling such plastics by thermally breaking them down to their molecular building blocks (oligomers), which can then be re-constituted to create new virgin-quality materials. Our technology, honed over a decade of R&D, delivers high conversion yields of 65-75% and generates chemical feedstocks that have been qualified for the circular economy by multiple petrochemical companies globally,” he adds, noting that the technology has attracted significant interest from Bengaluru.
According to a release from the company, the technology represents a major advancement over the current mechanical recycling methods which primarily convert waste plastics into low-quality granules with properties inferior to virgin plastics. Mechanical recycling is also not configured to viably process contaminated plastics which have high amount of moisture, dirt, food residues and mixed resins. PolyCycl’s technology is designed to process contaminated dirty polyolefin plastics diverted from landfills.